Cosa vuol dire controllo numerico?
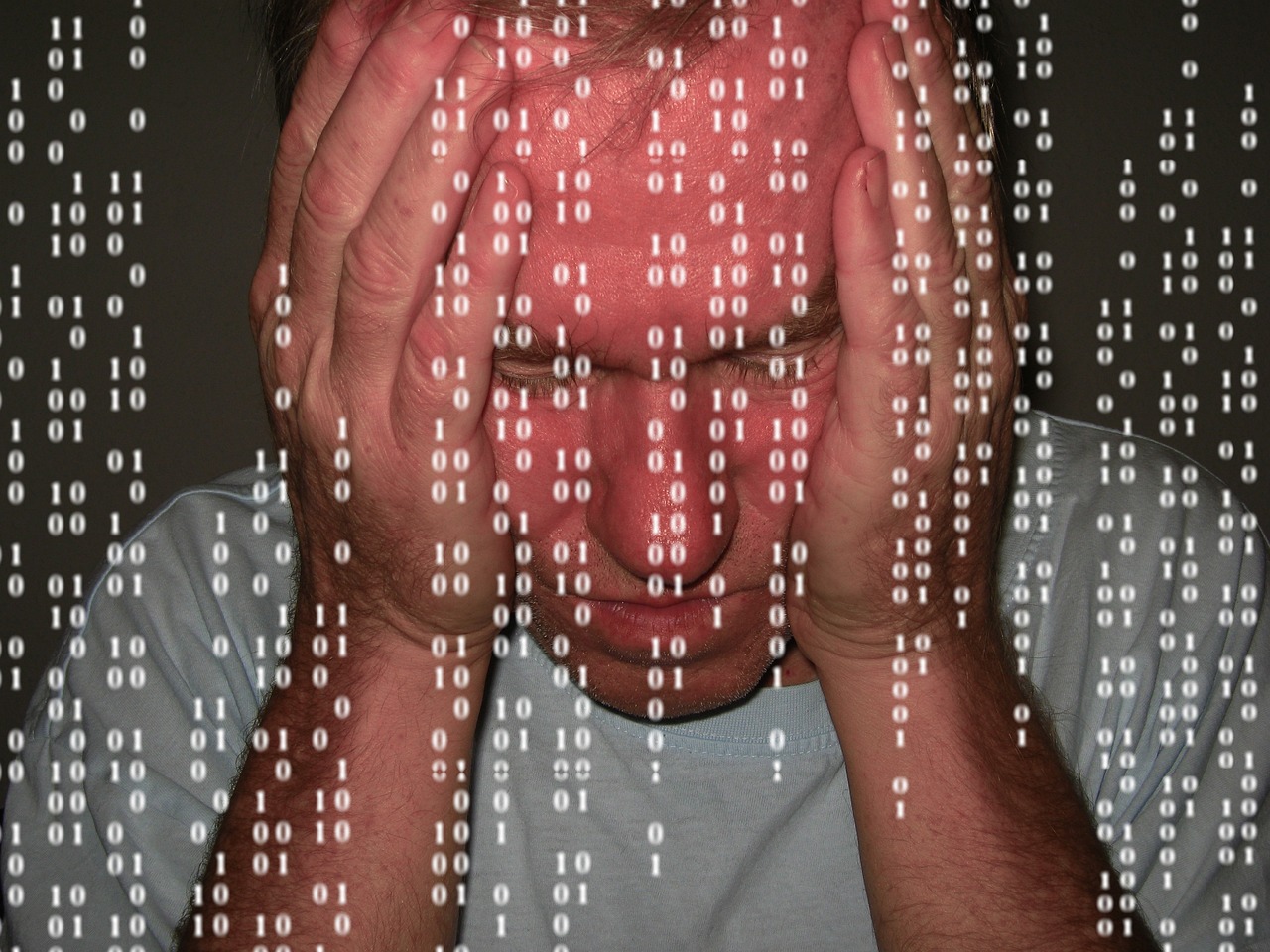
Cosa vuol dire controllo numerico?
Il controllo numerico è un sistema di gestione e controllo degli strumenti di lavorazione, come ad esempio macchine utensili e robot industriali, che si basa su un linguaggio di programmazione, solitamente abbreviato come CNC (Computer Numerical Control).
Il sistema CNC rappresenta uno sviluppo tecnologico fondamentale nell'ambito dell'automazione industriale. Grazie al controllo numerico, è possibile programmare in maniera precisa e automatica le operazioni eseguite da macchine come torni, fresatrici, trapani, stampanti 3D e molti altri dispositivi, riducendo al minimo gli errori e ottimizzando il processo produttivo.
Attraverso appositi programmi, i tecnici e gli operatori possono definire in modo dettagliato le sequenze di movimento e le azioni che il sistema deve eseguire. Le informazioni sono inserite attraverso un'apposita interfaccia, che traduce il codice di programmazione in segnali elettrici per i vari componenti della macchina.
Il controllo numerico offre numerosi vantaggi rispetto ai metodi di lavorazione convenzionali. Innanzitutto, garantisce elevati livelli di precisione e ripetibilità, permettendo di ottenere prodotti finiti con tolleranze molto strette. Inoltre, consente di automatizzare interamente il processo produttivo, riducendo al minimo la necessità di intervento umano e aumentando la velocità di produzione.
Un altro vantaggio del sistema CNC è la possibilità di programmare operazioni complesse e particolari, come tagli inclinati, scanalature intricate o contouring a 5 assi. Il controllo numerico permette di gestire in modo preciso e coordinato i movimenti degli utensili, ottenendo risultati che sarebbero difficilmente realizzabili con soluzioni manuali.
In conclusione, il controllo numerico rappresenta una tecnologia indispensabile nel settore dell'automazione industriale. Grazie a questa tecnica di programmazione, è possibile ottenere lavorazioni precise, veloci ed efficienti, riducendo al minimo gli errori e migliorando la produttività complessiva.
Cosa si intende per controllo numerico?
Il controllo numerico è una tecnologia utilizzata nell'ambito dell'automazione industriale per controllare e gestire macchine utensili, robot e altri dispositivi. Consiste nell'utilizzo di un sistema informatico, chiamato controllore numerico, che interpreta le istruzioni generate dal programma e le traduce in movimenti e azioni precise dei dispositivi meccanici.
Il controllo numerico è stato introdotto negli anni '50 come una soluzione avanzata per automatizzare e migliorare il processo di produzione. Grazie alla sua affidabilità e precisione, ha rivoluzionato l'industria manifatturiera, consentendo la produzione di pezzi complessi in tempi più rapidi e con una maggiore precisione.
Le macchine utensili controllate numericamente, come torni, fresatrici e macchine a controllo numerico (CNC), sono dotate di un sistema di controllo numerico che gestisce i movimenti degli assi e controlla il funzionamento di utensili e accessori. Attraverso l'uso di un programma specifico, che può essere scritto manualmente o generato da software CAD/CAM, è possibile definire con precisione il percorso e la sequenza delle operazioni da eseguire.
L'utilizzo del controllo numerico presenta numerosi vantaggi. Innanzi tutto, permette una maggiore automazione e un'efficienza operativa superiore, riducendo al minimo l'intervento umano nel processo di produzione e garantendo una maggiore coerenza e ripetibilità dei risultati. Inoltre, consente di lavorare con materiali più duri e complessi, grazie alla precisione e alla potenza delle macchine a controllo numerico.
Un'altra caratteristica fondamentale del controllo numerico è la possibilità di apportare modifiche al programma in qualsiasi momento, senza dover modificare fisicamente le macchine. Questo consente una maggiore flessibilità e adattabilità alle esigenze di produzione in continua evoluzione.
In conclusione, il controllo numerico rappresenta una tecnologia avanzata che ha rivoluzionato l'industria manifatturiera. Grazie alla sua capacità di gestire precisione, velocità ed efficienza, è diventato un elemento fondamentale per migliorare la produttività e la qualità dei prodotti.
Quanto guadagna un operaio CNC?
L'operaio specializzato nel controllo numerico (CNC) svolge un ruolo fondamentale nel settore industriale, operando macchinari ad alta tecnologia per la produzione di pezzi meccanici. La sua competenza nel controllo delle macchine CNC e la precisione nel lavoro svolto sono essenziali per garantire risultati di qualità.
Quanto riguarda il guadagno di un operaio CNC, è importante tenere in considerazione diversi fattori, come l'esperienza professionale, le competenze acquisite, la localizzazione geografica e la dimensione dell'azienda per cui lavora.
Per un operaio CNC junior, senza esperienza specifica nel settore, il salario medio si attesta intorno ai 1.500-1.800 euro al mese. Tuttavia, man mano che l'esperienza aumenta, così come le competenze e la capacità di gestire macchinari più complessi, è possibile ottenere una crescita salariale.
Per un operaio CNC con esperienza, è possibile guadagnare in media dai 2.000 ai 2.500 euro al mese. Le abilità avanzate nel controllo delle macchine CNC e la capacità di lavorare su pezzi di alta precisione possono influire positivamente sullo stipendio.
È fondamentale tenere conto anche della localizzazione geografica dell'operaio CNC. Ad esempio, in alcune regioni italiane, come Lombardia o Emilia-Romagna, i salari possono essere più elevati grazie alla presenza di importanti aziende del settore.
Infine, la dimensione dell'azienda per cui lavora l'operaio CNC può influire sul guadagno. Le grandi aziende industriali tendono ad offrire salari maggiori rispetto alle piccole e medie imprese.
In conclusione, il guadagno di un operaio CNC dipende da vari fattori come l'esperienza, le competenze, la localizzazione geografica e la dimensione dell'azienda. Tuttavia, in generale, un operaio CNC può guadagnare tra i 1.500 e i 2.500 euro al mese, con possibilità di crescita salariale in base all'esperienza e alle capacità acquisite nel tempo.
Chi ha inventato il controllo numerico?
Il controllo numerico è una tecnologia che permette di controllare e gestire le macchine tramite programmi informatici. Esso ha rivoluzionato il settore manifatturiero, consentendo la produzione di pezzi altamente precisi e complessi. Ma chi ha inventato il controllo numerico?
La paternità di questa innovazione va attribuita a John T. Parsons, un ingegnere e inventore americano. Negli anni '40, Parsons avviò una società chiamata "Parsons Corporation" insieme alla sua moglie per sviluppare un sistema che automatizzasse la lavorazione dei pezzi per aerei. Egli si rese conto che sarebbe stato più efficiente e accurato controllare le macchine tramite un sistema di controllo numerico, invece di utilizzare i tradizionali metodi manuali.
Parsons collaborò quindi con Frank L. Stulen e Norman F. Carter, entrambi ingegneri elettrici, per sviluppare il primo prototipo di controllo numerico nel 1949. Questo prototipo venne installato su una fresa, rendendo possibile l'esecuzione di complesse operazioni di fresatura in modo completamente automatico.
Il sistema di controllo numerico di Parsons era basato su una serie di fogli di carta perforata, che contenevano le istruzioni per la macchina. Ogni foro sulla carta rappresentava un comando specifico da eseguire. Questo sistema fu chiamato "gettapercussion punch-card control" e rappresentò l'embrione del moderno controllo numerico.
La vera innovazione arrivò però nel 1952, quando Parsons e Stulen svilupparono il primo controllo numerico completamente digitale, utilizzando un computer IBM per gestire le operazioni. Questo sistema permetteva di entrare le istruzioni direttamente in un computer, senza bisogno di ricorrere ai fogli di carta perforata.
Il controllo numerico si diffuse rapidamente tra le industrie manifatturiere, permettendo di automatizzare e migliorare la precisione di molte operazioni, come fresatura, tornitura e saldatura. Nel corso degli anni, questa tecnologia si è evoluta ulteriormente, grazie all'uso di computer sempre più potenti e sofisticati algoritmi di controllo.
Oggi, il controllo numerico è ampiamente utilizzato in molti settori industriali, come l'aeronautica, l'automotive e l'elettronica. Grazie a questa innovazione, è possibile realizzare prodotti di altissima qualità e complessità, apportando notevoli miglioramenti nell'efficienza e nella precisione della produzione.
Quali sono i 5 assi di un CNC?
Un sistema di controllo numerico computerizzato (CNC) viene utilizzato per il movimento e il controllo di macchine utensili, come torni, fresatrici e stampanti 3D. Una delle caratteristiche principali di un sistema CNC è la possibilità di controllare diversi assi di movimento. Ma quali sono i 5 assi di un CNC?
I 5 assi di un CNC includono:
- Asse X: è l'asse orizzontale che si estende lateralmente. È responsabile del movimento laterale dell'utensile o della tavola di lavoro.
- Asse Y: è l'asse verticale che si estende in alto e in basso. È responsabile del movimento in altezza dell'utensile o della tavola di lavoro.
- Asse Z: è l'asse longitudinale che si estende avanti e indietro. È responsabile del movimento in profondità dell'utensile o della tavola di lavoro.
- Asse A: è l'asse di rotazione attorno all'asse X. Permette di ruotare l'utensile o la tavola di lavoro in una direzione specifica.
- Asse B: è l'asse di rotazione attorno all'asse Y. Permette di ruotare l'utensile o la tavola di lavoro in un'altra direzione specifica.
La combinazione di questi 5 assi offre al sistema CNC una vasta gamma di movimenti e di possibilità di lavorazione. Ciò consente di realizzare lavorazioni complesse e precise su una varietà di materiali.
Grazie alla possibilità di controllare i 5 assi, un CNC può eseguire operazioni come il taglio a contorno, l'incisione, la fresatura tridimensionale e molto altro ancora. La grande versatilità dei 5 assi consente di ottenere risultati di alta qualità e di eseguire compiti più complessi rispetto ai sistemi a 3 assi.
In conclusione, i 5 assi di un CNC, ovvero X, Y, Z, A e B, sono fondamentali per il controllo dei movimenti in una macchina utensile computerizzata. Questi assi consentono di ottenere lavorazioni più precise e complesse, aprendo la strada a infinite possibilità nel campo della produzione e della lavorazione industriale.
stai cercando lavoro?
Vuoi trovare un lavoro?
Vuoi trovare un lavoro?